The company KEM ONE, second European PVC producer, called upon LCI group to install on its site of Balan (01) two new steam production boilers 2x40 T/h tri-fuel (ethylene, evazol and natural gas on a burner), with economizer and condenser.
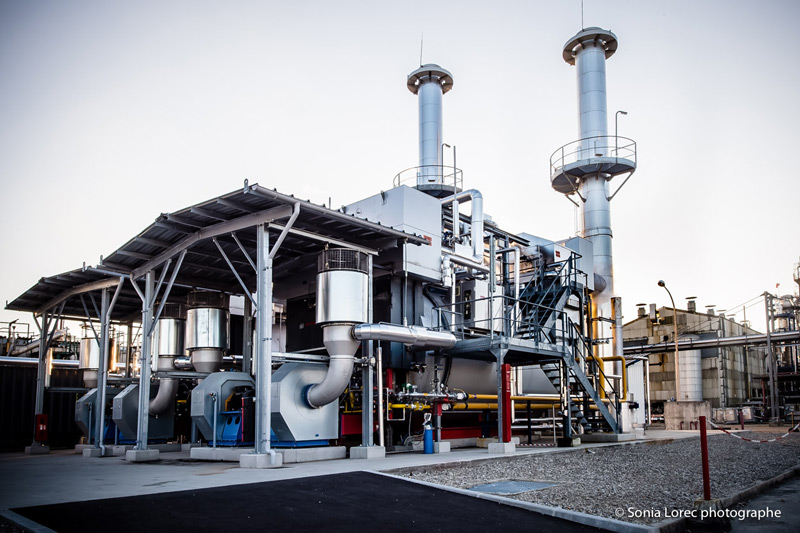
Through this investment, KEM ONE's objectives were clearly stated: to reduce the site's greenhouse gas emissions and energy consumption.
LCI group equipped the site with two new ultra-efficient steam production boilers to meet KEM ONE's environmental and economic objectives. Find out why and how KEM ONE was able to meet its ambitions!
Why replace the boilers at the KEM ONE site in Balan?
A strong commitment to energy savings
In addition to the desire to comply with regulatory changes in emissions standards (NOx, etc.), KEM ONE has a strong social responsibility to save natural resources.
This is why the installation of high efficiency boilers has become a priority. Measurements have confirmed an efficiency of over 102% on PCI, including the condenser, which is exceptional for an installation of this power and complexity.
An economic approach
Energy represents an important part of KEM ONE's costs, and the economic dimension of reducing energy bills naturally reinforced the choice of this investment.
The LCI group boilers, a condensed technology at the service of production performance
To carry out the transformation of its raw materials (gases & liquids) into finished products (solid plastics), KEM ONE needs to heat and cool.
For heating, the process uses steam from boilers, and for cooling, water from atmospheric cooling towers. Finally, not only the finished products, but also the water is purified by thermal treatment.
With the LCI group boilers, KEM ONE produces steam by vaporizing heated purified water. The heat is supplied by various fuels (natural gas, recycled process gas) and the pressurized steam production is distributed to the site via a network of pipelines.
The new boilers are associated with the installation of heat recovery systems, electronic speed controllers, etc., as well as the implementation of a specific organization that allows for the measurement and monitoring of energy performance, the identification and implementation of improvement measures, the optimization of the operation of the installations and the minimization of energy consumption.
Thanks to the installation of 2 new boilers in Balan, a quantified study has validated the achievement of the objectives set by KEM ONE:
- A 20% decrease in our energy consumption in 3 years
- A 75% decrease in nitrogen oxide (NOx) emissions by using very low emission burners
- A 10,000 t/year decrease in our GHG emissions (= carbon footprint of half of Balan)
- A 20% improvement in our energy efficiency, allowing a significant decrease in our fossil energy consumption
- A reduction in the electrical consumption of the boiler room equivalent to the annual consumption of 280 households
These figures confirm the choices made by KEM ONE in their race to modernize their industrial facilities in order to reduce their carbon footprint, improve the performance of their site, and ensure the sustainability of their activity.